1. Schrittmotorbetrieb
Schrittmotoren arbeiten durch sequentielles Ein- und Ausschalten mehrerer Spulen, die den Rotor umgeben, so dass die Welle magnetisch gezwungen wird, sich in diskreten Schritten zu drehen. Schritte von 0,9 bis 1,8 Grad sind durchaus üblich, was 400 bis 200 Schritte pro voller Umdrehung der Welle ergibt.
Wie im wirklichen Leben kann nichts ohne Zeitverzögerung von einem Zustand in einen anderen übergehen. Im Fall des Schrittmotors braucht der Strom, der durch die einzelnen Spulen fließt, und damit das Magnetfeld, das den Rotor zu jedem Drehschritt antreibt, eine gewisse Zeit, um wirksam zu werden. Das liegt daran, dass die Spule eine Induktivität hat (ausgedrückt in Henries, abgekürzt mit dem Buchstaben H), die eine natürliche Tendenz hat, dem Fluss eines sich schnell ändernden Stroms zu widerstehen. Eine größere Spuleninduktivität führt zu einer langsameren Stromänderung und somit zu einer langsameren Ausdehnung und Kontraktion des Magnetfelds.
Das maximale Drehmoment, das ein Schrittmotor erreichen kann, liegt vor, wenn der Motor mit einer erregten Wicklung stillsteht. Dieser Wert kann auf dem Datenblatt eines Schrittmotors als "Haltemoment" angegeben sein. Je schneller jede Spule ein- und ausgeschaltet wird, um die Welle in Drehung zu versetzen, desto kürzer ist die Zeit, in der jede Spule ihre volle magnetische Anziehungskraft auf den Rotor ausüben kann, wodurch sich das Gesamtdrehmoment verringert. Diese Beziehung zwischen Drehzahl und Drehmoment ist weitgehend umgekehrt proportional.
Im folgenden Beispiel wird die Ladezeit für drei Spulen angezeigt, wenn die angelegte Spannung von 0 V auf 40 V abgestuft wird. Während alle drei Spulen leicht die volle Stromgrenze von 5 Ampere (A) erreichen können, variiert die benötigte Zeit für jede Spule. Die 4-Milli-Henry-Spule (mH) (blaue Spur) benötigt doppelt so lange, um den vollen Strom zu erreichen, als die 2-mH-Spule (grüne Spur), und die 8-mH-Spule (rote Spur) benötigt wieder doppelt so lange:
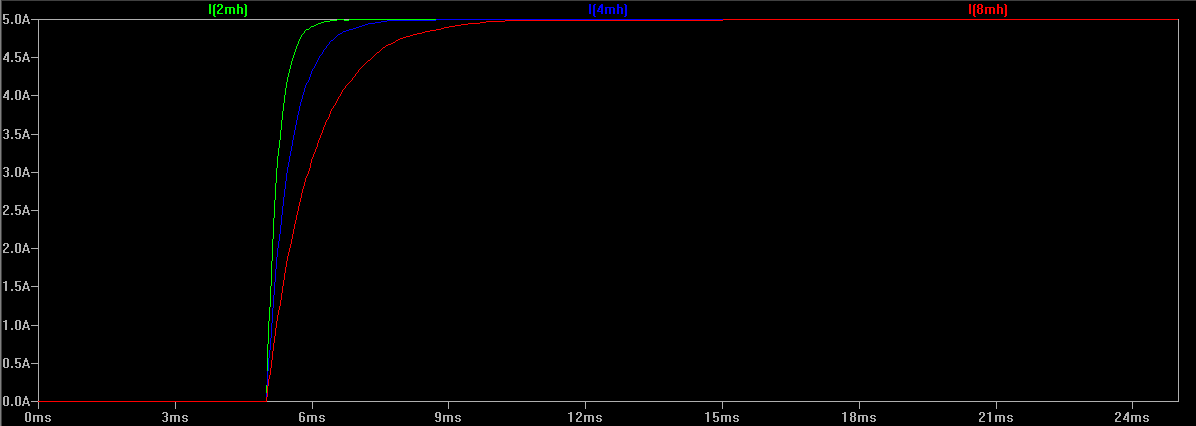
Wenn die Geschwindigkeit, mit der die Sprünge an die Spulen angelegt werden, deutlich kürzer ist als die Anstiegszeit, ist es leicht zu erkennen, dass die Wicklung weniger Zeit hat, die volle magnetische Anziehungskraft auf den Rotor zu erreichen, und somit wird das maximale Drehmoment eingeschränkt. Im folgenden Beispiel kann die 2 mH-Spule die volle 5 A-Grenze erreichen, bevor die Schrittspannung entfernt wird, die 4 mH- und 8 mH-Spulen jedoch nicht:
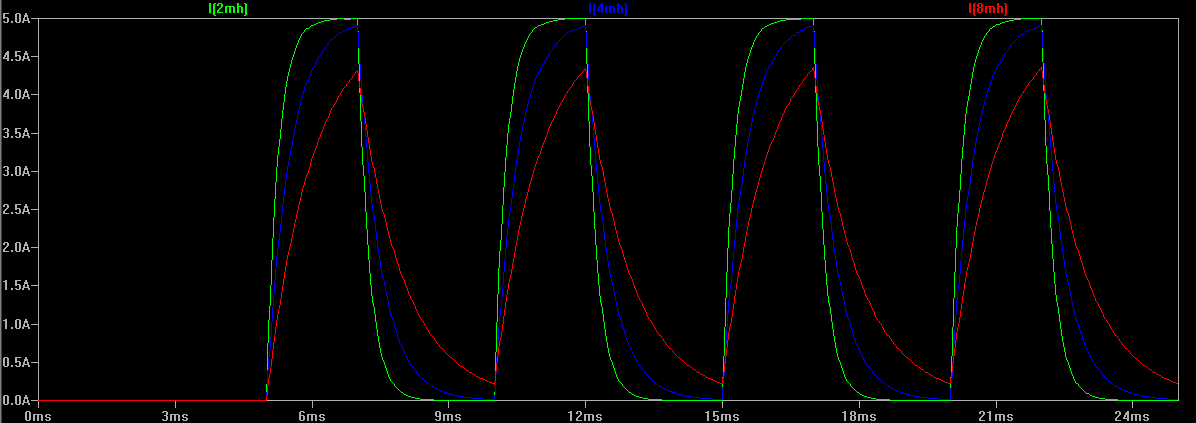
Die gängige Methode zur Verbesserung der Motordrehzahl bei gleichbleibendem Drehmoment besteht darin, die Geschwindigkeit zu erhöhen, mit der sich das Magnetfeld der Motorspulen ausdehnen und zusammenziehen kann. Der einfachste Weg, dies zu erreichen, besteht darin, die Versorgungsspannung zu erhöhen, um den Strom in jeder Wicklung zu zwingen, viel schneller anzusteigen und abzufallen. Eine schnellere Magnetisierungszeit führt zu schnelleren Schrittgeschwindigkeiten und verbessert das Drehmoment bei höheren Geschwindigkeiten, was in einem CNC-System natürlich wünschenswert ist.
Wenn man dasselbe Beispiel wie oben verwendet, aber die Schrittspannung auf 80 V erhöht, kann man sehen, dass alle drei Spulen jetzt ganz leicht das Maximum von 5 A erreichen können:
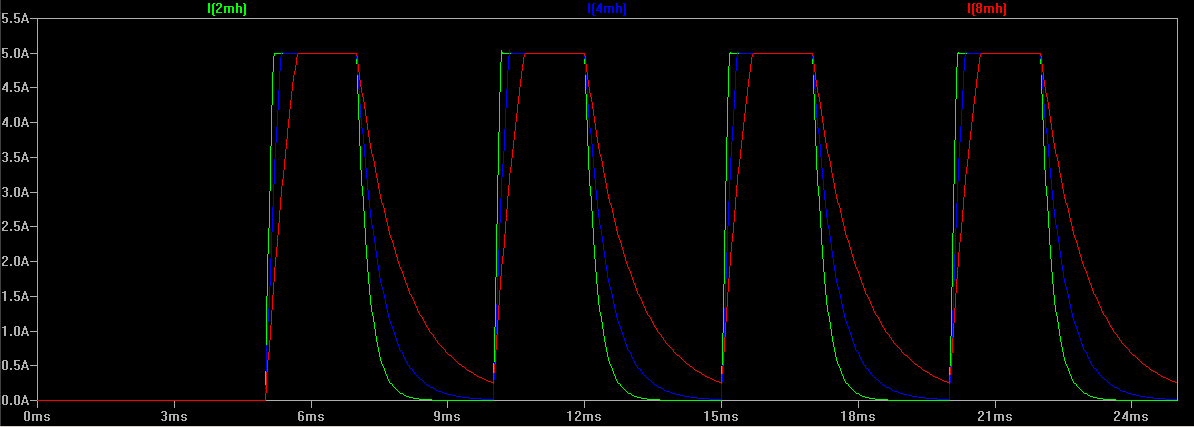
Eine höhere Antriebsspannung muss jedoch sorgfältig gehandhabt werden, da eine höhere Spannung den Stromfluss in jeder Spule erhöht, was zu einem entsprechenden Temperaturanstieg der Wicklung führt. Ein übermäßiger Temperaturanstieg in der Wicklung führt schließlich zu einer Überhitzung und zum Ausfall des Motors.
In den meisten schrittmotorbasierten CNC-Systemen ist die Spannung der Stromversorgung für den Schrittmotor-Treiber um mehrere Größenordnungen höher als die Spannung des Motors selbst. Ein typischer NEMA23-Schrittmotor hat vielleicht nur eine Nennspannung von ein paar Volt, aber die Stromversorgung und der Treiber können mit 48 VDC oder mehr betrieben werden.
Fast alle modernen Schrittmotortreiber auf dem Markt sind heute Konstantstrom-Typen. Das heißt, der Strom, der an jede Wicklung angelegt wird, ist fest, unabhängig davon, wie viel Spannung angelegt wird. Die meisten Treiber erreichen dies, indem sie den Strom, der durch die Motorwicklungen fließt, überwachen und die Ausgänge mit einer sehr hohen Frequenz schnell ein- und ausschalten, um diesen Strom beizubehalten. Je nach den verwendeten Treibern kann es sogar möglich sein, dieses hochfrequente Pfeifen in den Motoren selbst zu hören, wenn diese stillstehen. Da die Spannung schnell ein- und ausgeschaltet wird, um den Wicklungsstrom auf einem annähernd festen Wert zu halten, werden diese Arten von Treibern auch als "Chopper-Drive" bezeichnet.
2. Auswahl einer Stepper-Stromversorgung
Eine höhere Spannung steht zwar in direktem Zusammenhang mit einer höheren Geschwindigkeit und einem höheren Drehmoment, aber es gibt natürlich eine Grenze, ab der eine höhere Versorgungsspannung nicht mehr von Vorteil ist. Die erste Grenze für die maximale Versorgungsspannung ist wahrscheinlich diejenige, die der Schrittschalttreiber selbst aushalten kann. Dieser Wert sollte im Datenblatt des Steppertreibers angegeben sein, und ein Überschreiten dieser Spannung führt zur Zerstörung des Treibers. Idealerweise sollte die Versorgungsspannung so gewählt werden, dass diese maximale Spannung um etwa 10 % unterschritten wird. Wenn z.B. ein Schrittschalttreiber eine Vmax von 80 VDC hat, sollte die maximale Versorgungsspannung auf 72 VDC begrenzt werden.
Wie bereits erwähnt, führt eine zu hohe Motorversorgungsspannung auch zu einem übermäßigen Wärmeanstieg in den Motorwicklungen, was schließlich zu einem Ausfall des Motors durch Überhitzung führen kann. Eine häufig verwendete Gleichung zur Bestimmung der maximalen Spannung, um einen übermäßigen Wärmeanstieg zu vermeiden, ist die Quadratwurzel der im Motordatenblatt angegebenen Wicklungsinduktivität (ausgedrückt in Mill-Henry) und multipliziert mit 32. Wählt man zum Beispiel einen Schrittmotor mit einer Spuleninduktivität von 4 mH, so ergibt sich eine maximale Versorgungsspannung von 32 x SQRT (4) = 64 VDC.
In vielen Schrittmotordatenblättern finden sich auch Drehzahl-Drehmoment-Kurven, die oft für verschiedene Versorgungsspannungen aufgezeichnet sind. Bei der Betrachtung der Diagramme kann man feststellen, dass eine Erhöhung der Versorgungsspannung um den Faktor zwei nicht zu einer entsprechenden Verbesserung von Drehzahl/Drehmoment im gleichen Maße führt. Wenn der Betrieb eines Schrittmotors mit 64 VDC wenig bringt, kann dies dazu beitragen, die vorgeschlagene Versorgungsspannung auf 32 VDC zu beschränken, was auch dazu beiträgt, die übermäßige Erwärmung der Motorwicklungen zu minimieren.
Ein weiterer zu berücksichtigender Faktor ist die Stromstärke des Netzteils. Dieser Wert ergibt sich aus dem Nennstrom der Motorwicklung und daraus, ob die Motorwicklungen in Reihe oder parallel geschaltet sind; beide Angaben sollten im Datenblatt des Motors aufgeführt sein. Eine gute Faustregel ist, den Nennstrom der Stromversorgung auf 2/3 des Phasennennstroms des Schrittmotors zu bemessen, wenn die Wicklungen parallel geschaltet sind, oder auf 1/3 des Nennstroms, wenn sie in Reihe geschaltet sind. Für einen parallel geschalteten Schrittmotor mit einem Nennstrom von 4 A muss die Stromversorgung also mindestens 2,7 A bzw. 1,3 A bei einer Reihenschaltung betragen. Der Gesamtnennstrom des gesamten Systems ergibt sich dann aus der Summe der Stromanforderungen aller Schrittmotoren.
3. Resonanz
Motorresonanz tritt auf, wenn die Geschwindigkeit, mit der die Schritte an die Wicklungen angelegt werden, der Eigenfrequenz des Motors selbst entspricht. Wenn die Schritte über einen längeren Zeitraum mit dieser Rate angelegt werden, fällt das Drehmoment drastisch ab, und der Motor kann zum Stillstand kommen oder sich sogar in beliebige Richtungen drehen. Einige Schrittmotor-Datenblätter enthalten Diagramme des Verhältnisses zwischen Drehmoment und Drehzahl und zeigen eine Senke im Diagramm, in der wahrscheinlich eine Resonanz auftritt. Es ist zu beachten, dass diese im Datenblatt angegebene Resonanzspitze nur für den Motor selbst gilt - sobald der Motor mit anderen Komponenten gekoppelt ist (z. B. in einem CNC-System), kann sich die Resonanzfrequenz ändern oder es können sogar mehrere neue Resonanzen auftreten.
Es gibt mehrere Methoden, um die Auswirkungen der Resonanz zu kontrollieren, alle mit unterschiedlichem Grad an Komplexität, Wirksamkeit und Nebenwirkungen:
-
Der Mikroschrittbetrieb kann zur Verringerung der Resonanz beitragen, indem zwischen den einzelnen Schritten kleinere Stromsprünge verwendet werden. Diese kleineren Stromsprünge verursachen ein geringeres Klingeln im Motor und in den Wicklungen und somit eine geringere Erregung am Resonanzpunkt.
-
Eine sehr einfache Methode zur Verringerung der Resonanz ist es, den Motor nie über einen längeren Zeitraum mit einer bestimmten Frequenz zu betreiben, sondern immer über die Resonanzspitze zu beschleunigen oder abzubremsen.
-
Eine Erhöhung der Trägheitslast dämpft unerwünschte Resonanzen auf Kosten eines gewissen Drehmoments und möglicherweise einer gewissen Genauigkeit. Es können elastomere Motorlager, Wellenkupplungen oder Lagerhalterungen verwendet werden.
-
Fortschrittlichere Schrittmotorantriebe können zwischen verschiedenen Schrittmodi umschalten, so dass die Resonanzspitze bei bestimmten Betriebsgeschwindigkeiten verwaltet wird. Es gibt auch Systeme, bei denen die Wicklungen elektrisch belastet werden, was eine ähnliche Wirkung wie die oben beschriebene mechanische Dämpfung hat.
4. Mikroschritte (engl. microstepping)
Ein Schrittmotor, bei dem jede Wicklung sequentiell voll erregt wird, arbeitet im Vollschrittmodus. Das heißt, die maximal mögliche Drehungsauflösung für diesen Motor entspricht der Anzahl ganzer Schritte, für die der Motor hergestellt wurde (z. B. 200 Schritte pro Umdrehung für einen Motor mit 1,8 Grad/Schritt). Wenn jede Wicklung erregt wird, taktet der Rotor vollständig von einer Raste zur nächsten.
Eine zusätzliche Rotationsauflösung eines Schrittmotors kann durch Mikroschrittbetrieb erreicht werden, wobei der in jede Wicklung fließende Strom im Wesentlichen in diskreten Zwischenschritten "gerafft" werden kann. Dies führt dann dazu, dass der Rotor allmählich jede Drehung überbrückt, anstatt den vollen Sprung von einem Schritt zum nächsten zu machen.
Das Mikroschrittverfahren wird in der Regel in Vielfachen von 2 (4x, 8x, 16x, 32x usw.) durchgeführt. Ein Antrieb, der auf 4-fachen Mikroschrittbetrieb eingestellt ist, teilt beispielsweise jeden Schritt in vier diskrete Stromstufen in den Motorwicklungen auf, was eine Verbesserung der Rotationsauflösung um den Faktor vier bedeutet. Dies bedeutet natürlich, dass für eine typische Schritt-/Richtungssteuerungsschnittstelle viermal so viele Schrittimpulse erzeugt werden müssen, damit sich der Motor um denselben Betrag bewegt, wenn er im Vollschrittmodus betrieben wird. Damit sich der Motor mit der gleichen Geschwindigkeit dreht, muss auch die Rate, mit der die Impulse an den Antrieb angelegt werden, viermal so schnell sein.
Bei niedrigen Drehzahlen führt der Mikroschrittbetrieb sogar zu einem etwas höheren Drehmoment als der Vollschrittbetrieb. Dies ist auf die geringeren Stromänderungen zwischen den Zwischenschritten zurückzuführen, die dazu führen, dass weniger Energie zur Erregung von Eigenresonanzen im Motor verschwendet wird. Mit zunehmender Drehzahl nimmt das Drehmoment jedoch in ähnlicher Weise ab wie beim Vollschrittbetrieb.
Die weitere Erhöhung des Mikroschrittgrades führt jedoch irgendwann zu einigen Einschränkungen in der Praxis. Die Erzeugung von Schrittimpulsen, insbesondere bei Verwendung des Parallelanschlusses, ist in ihrer Frequenz begrenzt. Dies führt zwangsläufig zu einer Begrenzung der Höchstgeschwindigkeit, mit der ein Frequenzumrichter gesteuert werden kann. Bei einem hohen Grad an Mikroschrittbetrieb führt dies zu einer unannehmbar langsamen Drehzahl des Motors.
Übermäßig hohe Mikroschrittraten haben keinen wirklichen Nutzen, wenn die resultierende Genauigkeit zu gering ist, um mechanisch nützlich zu sein. Ein Motor mit 1,8 Grad pro Schritt und 16-facher Mikroschrittgeschwindigkeit kann theoretisch 0,1125 Grad pro Schritt erreichen. In Verbindung mit einer 20-TPI-Leitspindel sollte dies zu einer Positionsauflösung von 0,000016" oder 0,0004 mm führen. In der Realität ist es unglaublich schwierig, eine so feine Steuerung zu erreichen. Alle Komponenten des CNC-Systems weisen Toleranzen und Gegenkräfte auf (Spiel in den Leitspindeln, Biegung in den Portalen, Rundlauf in der Spindel und im Schneidwerkzeug, Haftreibung im Schrittmotor selbst, Fehler in der Schrittmotorrastung usw.), die solche geringen Auflösungen völlig bedeutungslos machen. In der Praxis hat der Mikroschrittbetrieb mit Geschwindigkeiten von mehr als dem 4- oder 8-fachen auf einer CNC-Maschine mit Leitspindeln wenig Sinn. In einigen Fällen kann es sogar vorteilhafter sein, mit niedrigeren Mikroschrittraten oder sogar Vollschritten zu arbeiten und den Schrittmotor über ein Untersetzungsgetriebe zu betreiben, um die erforderliche Auflösung und Drehmomentsteigerung zu erreichen.
5. Offener und geschlossener Regelkreis (engl. open and closed loop)
In den einfachsten CNC-Systemen, die Schrittmotoren verwenden, erhält der Host-Computer und/oder der Schrittmotor-Treiber keine Rückmeldung vom Motor, dass er das gewünschte Ergebnis erreicht hat, wenn er den Befehl erhält, mit dem Schrittbetrieb zu beginnen. Die Software, der Treiber und der Endbenutzer gehen davon aus, dass der Motor korrekt arbeitet und die Achse die erwartete neue Position erreicht hat. Ein System, das auf diese Weise arbeitet, wird als "offener Regelkreis" bezeichnet, bei dem das Gerät am Ende der Signalkette (der Schrittmotor) dem Gerät am Anfang der Kette (dem Computer) nicht mitteilt, dass das Ziel erreicht wurde.
Eine weitere Verbesserung des Schrittmotors besteht darin, das System in einem "geschlossenen Kreislauf" zu betreiben. Dies wird erreicht, indem der Schrittmotor mit einem Drehgeber ausgestattet wird, dessen Positionssignal an ein Gerät weiter oben in der Signalkette zurückgegeben wird. Auf diese Weise kann die tatsächliche Position des Motors jederzeit mit der erwarteten Position verglichen und die Antriebsparameter in Echtzeit angepasst werden, um sicherzustellen, dass der Motor nicht zurückbleibt. Auf diese Weise können Steppersysteme mit geschlossenem Regelkreis eine bessere Geschwindigkeits- und Drehmomentleistung erzielen als Systeme mit offenem Regelkreis, da das System jede Abweichung von der Leistung des Steppers bei wechselnden Lasten ständig ausgleicht.
Basissysteme, die auf diese Weise arbeiten, können nur die Schleife zwischen dem Motor und dem Treiber schließen und die Software auf dem Host-Computer aus der Schleife herauslassen. Die Software gibt Schritt-/Richtungsimpulse an den nachgeschalteten Treiber aus, wie sie es normalerweise bei einem Betrieb im offenen Regelkreis tun würde. In diesen Fällen verfügen die Treiber in der Regel über einen Alarmausgang der Software signalisieren, dass sie anhalten soll, wenn die auf den Schrittmotor ausgeübte Last zu groß wird, als dass der Treiber sie ohne Schrittverlust ausgleichen könnte.
Fortschrittlichere Implementierungen des Closed-Loop-Betriebs bringen das Encodersignal den ganzen Weg zurück zum Host-Computer, erfordern aber einen viel höheren Hardware- und Software-Overhead, um das Encoder-Feedback und die Berechnung und Bereitstellung der Antriebskompensation zu verwalten.